

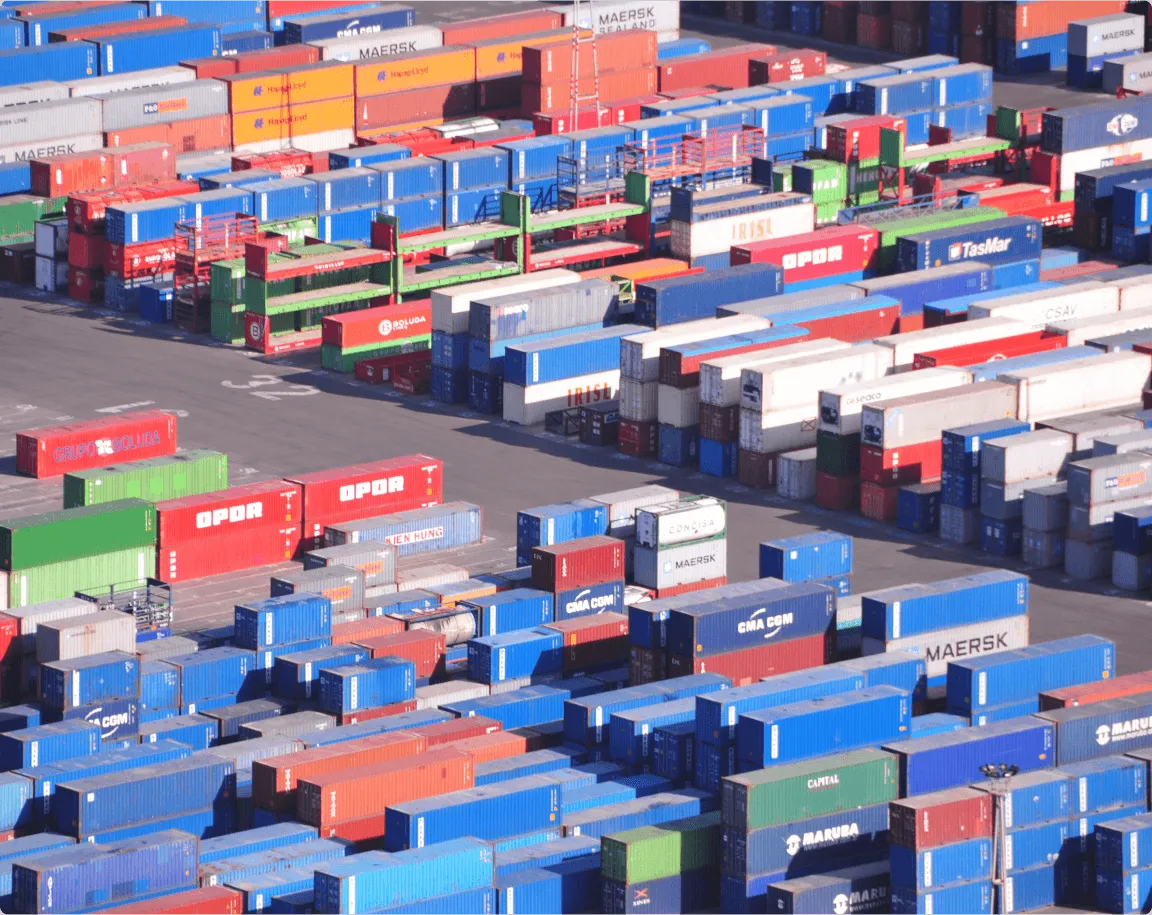
Meeting customer challenges with innovative solutions
In late summer 2022, Cowboy is rolling out a new version of their Odoo ERP internally to make it easier for them to track their orders and access information on delivery dates (arrival at warehouse, final delivery). To do this, Cowboy's Supply Chain team relies on OVRSEA data and must then integrate it manually into their ERP. The challenge of this integration is to automate this data transfer between Cowboy and OVRSEA. OVRSEA approached Cowboy to study the possibility of an API integration into their ERP in order to update the data automatically every morning. After a precise definition of the needs with Felix Fabich, Senior Supply Chain Engineer at Cowboy, Nader and Rémy, Product Manager and Software Engineer at OVRSEA, accompanied Vincent Van Rossem, Cowboy-Odoo developer, for the technical deployment of the integration.
The main use case that the integration had to address was the following: Cowboy wanted to display the status of goods shipments in real time (in progress, received, completed), to ensure follow-up and automatic actions in their Odoo ERP.
The main use case that the integration had to address was the following: Cowboy wanted to display the status of goods shipments in real time (in progress, received, completed), to ensure follow-up and automatic actions in their Odoo ERP.
Delivering exceptional results and benefits to our customers
- Synchronize Cowboy ERP with OVRSEA to eliminate the need to manually enter OVRSEA data into the ERP.
- Increase efficiency in tracking supplies to allow Cowboy to focus on higher value-added tasks.
- Integrate OVRSEA with Cowboy's ERP to have all data in one tool.
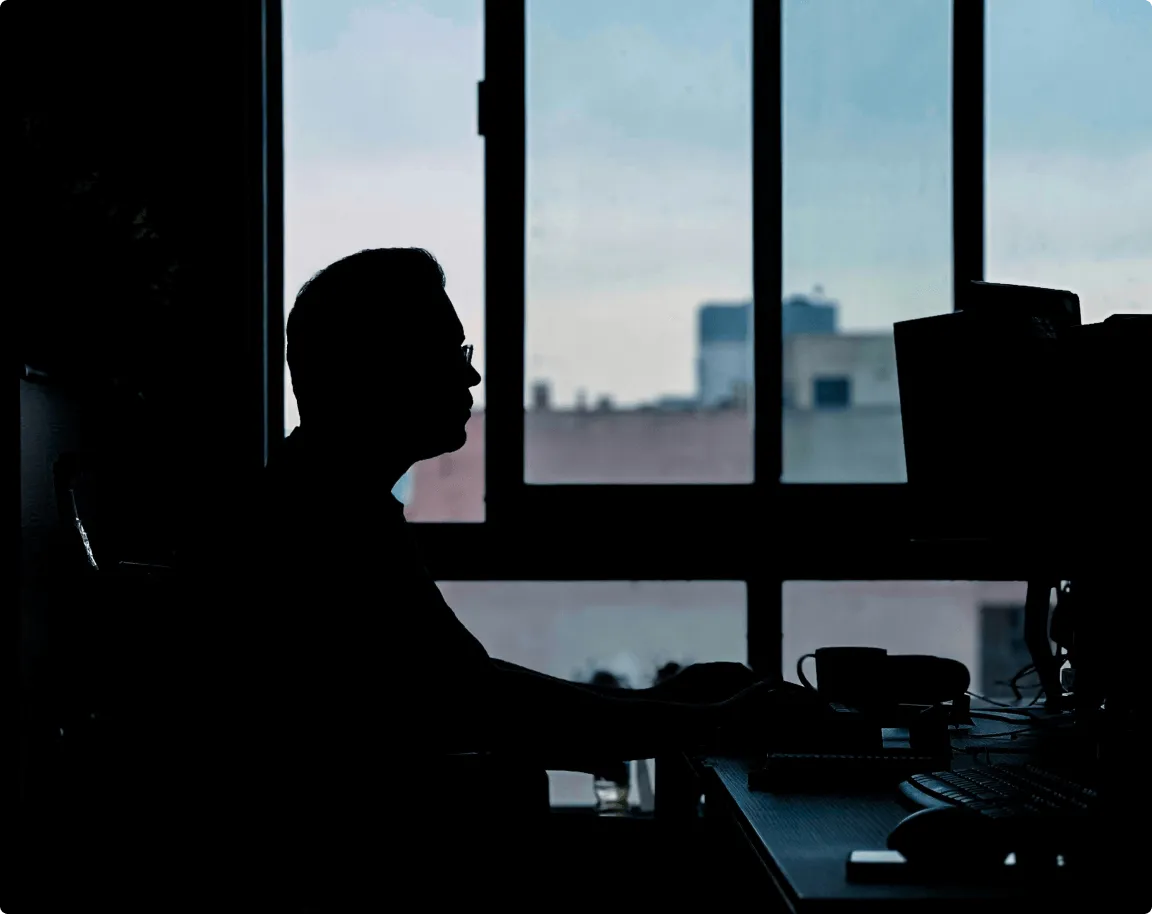
Project progress
Monitoring Cowboy's supplies prior to the implementation of the OVRSEA API integration
Prior to the deployment of the API Gateway, the data in Cowboy's ERP was updated manually. This data includes both the status of the shipment (in process, ready for shipment, shipped, received) and the estimated time of departure (ETD) or estimated time of arrival (ETA) of the goods.
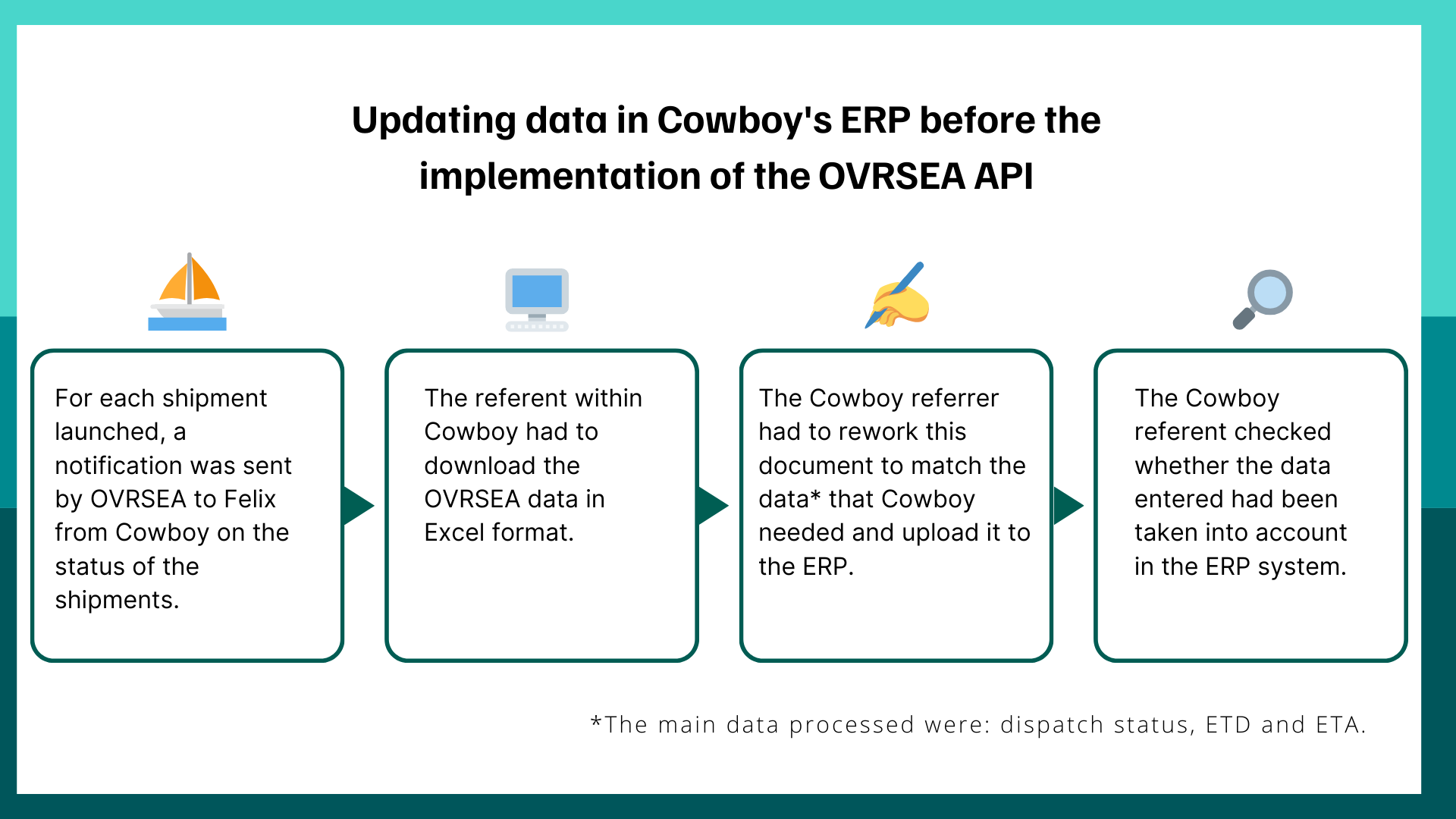
This organisation was working well but was exposing the company to human error due to the large volumes of data as well as manual data transfer from the Excel table to the ERP. But above all, this daily and redundant work wasted a lot of Cowboy's time.
“I would receive email notifications from OVRSEA when a shipment was about to be delivered to our factory and then I had to manually enter this information into our ERP. I had to click on a release button and then the goods movement would be executed in our ERP. This could lead to errors like validating the wrong quantity, opening the wrong shipment and it was very time consuming.”
- Felix Fabich, Senior Supply Chain Engineer at Cowboy
The impact of the OVRSEA API on Cowboy's supply tracking
The main benefit of the integration has been to give Cowboy's teams more visibility into their supply chain. The team can now focus on more value-added tasks and ensure that everything is on schedule. As a result of this integration, Cowboy has been able to spend more time analysing their shipments, shifting some of their air shipments to sea, and reducing their transportation expenses.
Today, the updating of data in the ERP is done automatically. The information provided is therefore reliable: Cowboy can have a perfect follow-up of its supplies, and on a single tool: its ERP. For example, when the supplier announces that 80% of outstanding orders will be shipped by Monday, Cowboy can cross-check the information. In terms of inventory, this integration also provides real-time information on the quantity of parts and materials in the factory, as well as in ships and aircraft in transit around the world.
“Visibility is very important for our planning team. Previously, they were always coming to me to see if a transfer had been done on time because everything was done manually. Now I don't have to worry about that and I can focus on other tasks that bring more benefit to the business.”
- Félix Fabich, Senior Supply Chain Engineer at Cowboy